4 Steps to Create a Successful Product: The Black Swamp Way
- Nathan Coles
- 5 days ago
- 4 min read
What does it really take to create a successful, high-quality product—one that’s consistent, inspiring to use, and built to last?
If you’ve ever played a great instrument and felt like it just works in your hands, it probably wasn’t by accident. Behind that experience is years of trial, iteration, problem-solving, and craftsmanship. At Black Swamp Percussion, we’ve spent three decades dialing in the process—so musicians can focus on their art.
Let’s peel back the curtain and explore the four steps that have guided our journey from a tiny startup to a trusted name in concert percussion.
Table of Contents
Don’t miss a new post 👇
A Brief History of Black Swamp Percussion
Black Swamp Percussion was founded in 1995 by percussionist and craftsman Eric Sooy. Back then, he had no employees, no fancy machines, and very little money—just a passion for sound and a drive to create better instruments.
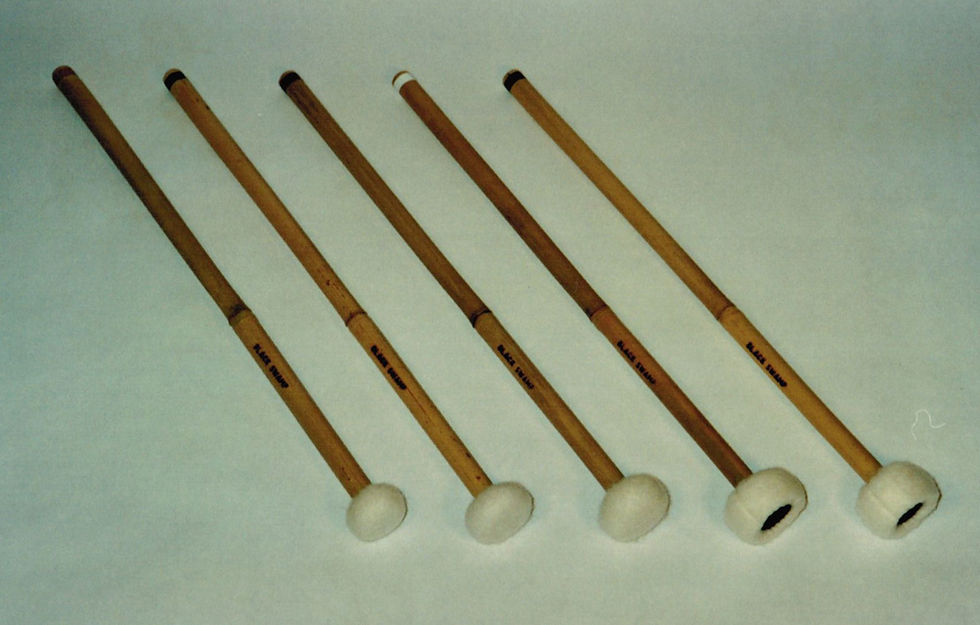
His journey started with a simple question: What’s missing? Digging through old catalogs from Lone Star and Steve Weiss, Eric noticed products that weren’t being made—or weren’t being made well. His first product? Bamboo timpani mallets. Getting straight bamboo was far more difficult then than it is today, and it took creative sourcing and a lot of grit to make it work.
From these humble beginnings, Eric built Black Swamp one instrument at a time, fueled by relentless curiosity and a refusal to settle for “good enough.”
Step 1: Identify the Opportunity
Every product begins with a spark—an observation that something is missing or could be better.

In the early days, Eric looked through industry catalogs and asked: What’s not being made that I could build? Sometimes it was about fulfilling a niche, other times about making a common tool perform better, sound better, or simply feel more inspiring in the hands of the player.
For example, when Black Swamp began designing its castanet machine, it wasn’t just about filling a gap—it was about reinventing a tool that wasn’t working well for musicians. That same mindset continues to drive every new product.
Step 2: Iterate Until It Works
This is where the real work begins.
After identifying the opportunity, it’s time for trial and error—lots of it. This step often involves prototyping, sourcing materials, tweaking designs, and going back to the drawing board again and again.
One castanet frame, for example, took years to get right. Parts didn’t fit quite right. Ideas worked on paper but failed in practice. It’s a slow grind. As Eric says,
“Every time I think I’m close to the finish line, I’ve months to go.”
But this process isn’t a bug—it’s the feature. Because iteration is where the details live. And in our world, the details are everything.
Step 3: Build the Process
Once a product works, you have to figure out how to make it consistently—and efficiently.
This means building custom tooling, creating fixtures, sourcing reliable parts, and documenting every step. Efficiency in manufacturing isn’t about cutting corners—it’s about eliminating variables and setting up systems that reduce human error.

Take our wood blocks, for instance. For years, we processed raw lumber ourselves—from jointing and planing to shaping each block. But eventually, we partnered with a local architectural wood supplier who could deliver pristine, pre-shaped maple blanks. The result? More consistency, less time waste, and a better final product.
Great process means fewer mistakes. And at Black Swamp, the goal is zero mistakes.
Step 4: Invest in Tools, People & Quality
You don’t make world-class instruments with second-rate tools. You also don’t make them without great people.
As Black Swamp grew, so did our investment in specialized equipment—some of it custom-designed just for our instruments. The goal? Make machines do the repetitive, precise work so that our people can focus on the tasks that require a human touch, like tuning temple blocks and pitch pairing castanets.
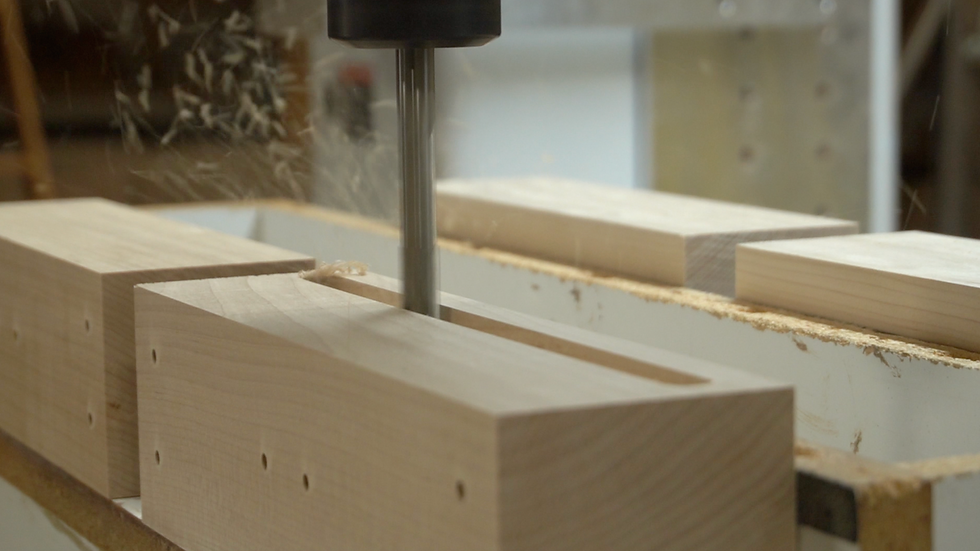
Eric calls it “the myth of the handmade.” Every craftsperson uses tools. The difference is in how well you use them. A CNC machine can be just as much a tool of craftsmanship as a chisel—if it’s wielded with intention.
And finally, we hold ourselves to high standards. We don’t settle for “good enough” or “no one will notice.” Every piece that leaves our shop reflects our values: artistry, integrity, and a refusal to compromise.
The Takeaway
Creating a successful product doesn’t happen overnight. It takes vision, persistence, patience, and pride in the process. After 30 years, we’ve learned that success isn’t just about making great instruments—it’s about making them better every time.
If you’re a builder, a musician, or just someone chasing your own version of excellence, remember: the details matter, and the process is the product.
Here’s to doing it right—even when it’s hard.
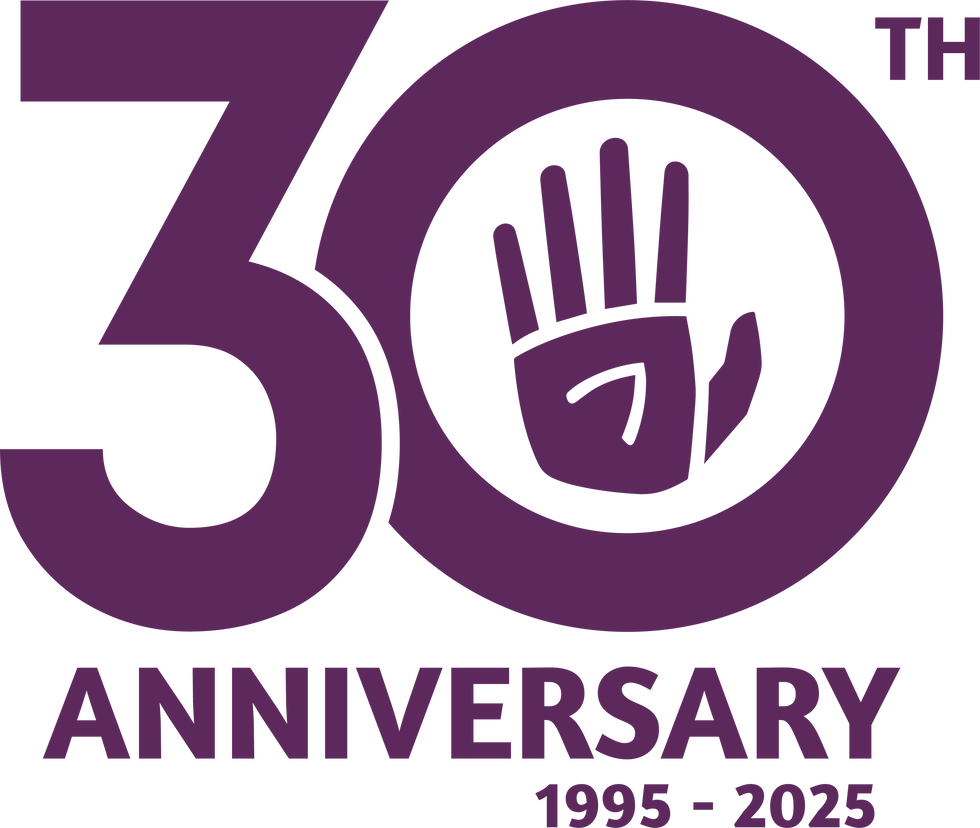
Join us as we celebrate our 30th Anniversary with limited edition products, exclusive merch, and behind the scenes looks like this!
Comments